Bien que l’emballage ne soit pas une des fonctions les plus importantes d’une entreprise, il s’agit d’une fonction stratégique qui peut donner une plus-value au produit. La vision classique consistait à investir peu dans l’emballage afin de ne pas augmenter substantiellement le coût de revient du produit.
Cependant, un emballage adéquat peut devenir un facteur de succès pour l’entreprise et, par le fait même, faire augmenter signifcativement ses revenus. Par exemple, un contenant de carton de deux litres, dans le cas de certaines marques de jus de fruits, peut être considéré comme un emballage très attrayant. Il s’agit alors pour le gestionnaire d’investir un montant qui pourra être récupéré à moyen terme, c’est-à-dire sur une période de un à trois ans.
Table de matières
Définition de l’emballage
L’emballage (Packaging ou Wrapping) est la façon de protéger les marchandises contre les dommages subis durant le transport, l’entreposage et la manutention. Très souvent, quand on parle d’emballage, un autre terme est utilisé : le conditionnement. En fait, le conditionnement comprend l’emballage, l’action de mettre la marchandise dans l’emballage ainsi que le calage. Le calage consiste à utiliser une ou des cales pour stabiliser et protéger un produit emballé.
Il existe quelques catégories d’emballages, comme l’emballage lié à l’entreposage, l’emballage lié au transport et l’emballage lié à la vente.
Catégories d’emballages
L’emballage lié à l’entreposage
L’emballage lié à l’entreposage sert à protéger le produit contre les intempéries telles qu’une variation de température ou encore les rayons ultraviolets du soleil.
Les sangles en polyester s’assèchent et, de ce fait, perdent de leur effcacité lorsqu’elles sont exposées trop longtemps au soleil. Pour cette raison, on doit les accrocher à un mur à l’abri du soleil ou les ranger dans des boîtes de carton après utilisation.
L’emballage lié à l’entreposage sert également à protéger le produit contre les dommages dus aux accrochages ou au manque d’attention. Ainsi, la fourche d’un chariot élévateur peut entrer en contact avec une boîte de carton renfermant des pièces en métal. Évidemment, la boîte de carton peut être recyclée. Toutefois, si les pièces en métal sont bien protégées, elles demeureront intactes.
Finalement, lorsque l’on stocke des vêtements pour une assez longue période (de 6 à 12 mois), on insère souvent dans les boîtes de carton ou les sacs en plastique des boules de naphtaline (boules à mites). Ainsi, les vêtements sont protégés contre les insectes ou les petits rongeurs.
Les produits d’emballage et de conditionnement les plus utilisés sont la boîte de carton, la feuille de polystyrène, le morceau de styromousse, le rouleau de polyéthylène, le ruban adhésif de toutes les dimensions ( de 1/4 pouce à 2 pouces), la sangle en acier ou en polyéthylène, le baril de 45 gallons (205 litres) en acier ou en plastique, le papier recyclé et la planche de bois.
L’emballage lié au transport
L’emballage lié au transport permet de protéger un produit contre les chocs qui peuvent survenir pendant son transport. Cet emballage dépend du type de produit, du nombre de transbordements effectués ainsi que de la variation climatique entre le lieu d’origine et la destination, y compris les périodes d’arrêt et de stockage.
À cette étape, on pourrait chercher à connaître le poids d’une boîte de carton remplie d’un produit X et destinée essentiellement au transport routier. Une fois ce poids calculé, on pourrait, en connaissant les dimensions de la palette qui servira d’unité de chargement pour les boîtes de carton, trouver le poids de cette même palette. Enfn, on pourrait connaître le poids de la marchandise (Cayouette, 2002) chargée dans une semi-remorque qui se déplacerait d’un point A à un point B (voir l’exemple 1).
Exemple 1
On veut déterminer le poids d’une boîte de carton ayant les dimensions suivantes : 8 po × 14 po × 12 po de haut. La densité
du produit à transporter est de 7 lb le pied cube. Le carton pèse 0,5 lb le pied carré.
La première chose à connaître est le nombre de pieds cubes que contient la boîte de carton. On connaît les dimensions de la boîte
(8 po × 14 po × 12 po), ce qui représente 1 344 po3 . Pour convertir les pouces cubes en pieds cubes, on utilise le facteur 1 728.

Ce qui veut dire que le poids de la marchandise dans la boîte de carton (si elle est remplie au maximum de sa capacité) sera
de 7 lb/pi3 × 0,78 pi3 = 5,46 lb.
Il nous reste maintenant à trouver le poids de la boîte de carton. On sait que le carton pèse 0,5 lb le pied carré. Comme la boîte a des dimensions de 8 po × 14 po, si l’on considère les 6 faces de la boîte, on obtient 752 po2. On sait que 1 pi2 correspond à 144 po2. En faisant une simple règle de 3, on trouve le poids de la boîte :
752 po2 = X
144 po2 = 0,5 lb
X correspond donc à 2,61 lb
Par conséquent, le poids de la boîte de carton et de la marchandise qu’elle contient est de 5,46 lb + 2,61 lb = 8,07 lb.
De plus, on sait que les palettes mesurent 40 po × 48 po. Le plancher de la palette se trouve à 6 po du sol, et on peut entreposer à une hauteur maximale de 4 pi. Quel sera le poids de la marchandise et des boîtes de carton sur la palette ?
Dans ce cas, la première chose à faire serait de dessiner un plan de la palette de 40 po × 48 po de façon à se servir le plus possible des 2 dimensions mentionnées ci-dessus. Il faut également tenir compte de la contrainte de la hauteur maximale de 4 pi. On sait déjà que l’on ne peut superposer plus de 3 boîtes de carton sur la palette, puisque chaque boîte a une hauteur de 12 po et que le plancher de la palette se trouve à 6 po du sol.
Le côté de la boîte qui mesure 8 po pourrait être placé du côté de la palette qui en fait 40 ; cette dimension serait alors utilisée à son plein potentiel avec 5 boîtes.
Le côté de la boîte qui mesure 14 po serait utilisé du côté de la palette qui en fait 48. On pourrait donc y mettre 3 boîtes pour un total de 42 po. En centrant les boîtes, on aurait donc 3 po d’espace libre à chaque extrémité des côtés de 48 po.
Si l’on fait le calcul, on obtient 5 × 3 = 15 boîtes, ce qui correspond aux dimensions de la palette. Sur le plan de la hauteur, on se retrouverait également avec 3 boîtes de haut, ce qui veut dire qu’au total, on entreposerait 45 boîtes sur chaque palette. (Ici, il va sans dire que, pour éviter les éboulements, la personne affectée à l’emballage devra nécessairement utiliser le nombre de sangles approprié.)
Par conséquent, le poids de la marchandise et des cartons entreposés sur la palette sera de : 8,07 lb/boîte × 45 boîtes = 363,15 lb par palette
Finalement, quel sera le poids total de la marchandise à l’intérieur de la semi-remorque si l’on tient compte des données suivantes ? La semi-remorque mesure 53 pi de long × 9 pi de large × 8 pi de haut ; les palettes sont disposées côte à côte sans séparateur dans la semi-remorque ; on peut superposer 2 palettes ; et chaque palette de bois pèse 40 lb.
En utilisant la dimension de 40 po de la palette dans le sens de la longueur, on peut placer 15 palettes dans la semi-remorque et on obtient, par le fait même, 2 palettes de large. Compte tenu de la superposition des palettes, on se retrouve avec 60 palettes à l’intérieur de la semi-remorque. Le poids total sera donc de : (60 palettes × 40 lb/palette) + (60 palettes × 363,15 lb/palette) = 24 189 lb
L’emballage lié à la vente
Habituellement, dans le cas de l’emballage lié à la vente, on fait appel à un comité présidé par le directeur du marketing ou de la publicité. On veut s’assurer que l’emballage est attrayant dans le but d’infuencer le comportement d’achat des consommateurs. Comme ce type d’emballage risque d’être stocké et transporté, on veille à le rendre encore plus protecteur.
Durant la conception de l’emballage d’un produit, il convient de toujours penser à utiliser des matières recyclables. Par exemple, dans certains restaurants-minute, on préfère employer du carton mince plutôt que de la styromousse, puisque cette dernière n’est pas aussi facilement recyclable. Comme on le sait, les matières recyclables permettent une réutilisation ; autrement, elles deviennent des déchets qui contribuent à remplir les sites d’enfouissement ou les incinérateurs.
Un autre facteur à considérer au cours de la conception d’un emballage consiste à savoir si l’on désire avoir un emballage qui sera utilisé de nouveau ou qui sera abandonné. L’emballage que l’on peut réutiliser entraîne un coût de revient moins élevé si l’on considère les unités vendues.
Cependant, l’acheteur devra tenir compte de l’espace additionnel nécessaire au stockage de cet emballage de même qu’à son entretien, car il subira des avaries en plus de l’usure. L’avantage d’un emballage neuf sur un emballage qui a déjà servi est que la présentation du produit demeure très soignée, mais son prix d’achat s’avère plus élevé.
Bref, un emballage inadéquat peut entraîner des coûts exorbitants comme le règlement d’un litige avec un transporteur ou un client ainsi que la perte d’un ou de plusieurs clients. L’exemple 2 propose le calcul du coût de l’emballage d’un produit.
Exemple 2
Nous allons essayer de déterminer le coût d’emballage du produit de l’exemple 1 en tenant compte du coût du matériel et du coût de la main-d’œuvre liés à cette opération.
Les spécifcations de l’emballage sont les suivantes :
- coût de la boîte de carton : 1,25 $ ;
- coût des étiquettes de la boîte de carton : 0,02 $ (2 par boîte) ;
- coût de la palette réutilisable : 24 $ (on estime la vie de la palette à 12 expéditions) ;
- coût de la pellicule plastique : 0,85 $ par palette ;
- temps requis pour la mise en boîte de carton : 3 minutes ;
- temps de montage de la boîte de carton : 1 minute ;
- temps requis pour la mise en palette : 45 secondes par boîte ;
- temps requis pour enrober la palette de pellicule plastique : 2,5 minutes ;
- coût de la main-d’œuvre : 0,35 $/minute.
On cherche le coût de l’emballage du produit sur la palette.
Les coûts du matériel sont les suivants :
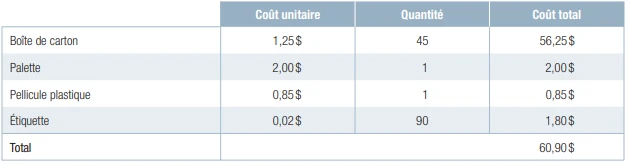
Les coûts de la main-d’œuvre sont les suivants :

Le coût total de l’emballage du produit sur une palette est donc de : 60,90 $ + 75,69 $ = 136,59 $
Si l’on connaît le prix du produit emballé, on peut savoir exactement quel pourcentage du coût total est consacré à l’emballage. Habituellement, un coût d’emballage ne doit pas dépasser 10 % du coût total d’un bien. Il est même souhaitable qu’il ne représente que 5 % du coût total afn d’obtenir plus rapidement un retour sur investissement.
Les fonctions de l’emballage
L’emballage du produit doit assurer 4 fonctions essentielles :deux fonctions techniques (logistique et protection) et deux fonctions commerciales (information et marketing).
La fonction logistique
L’emballage doit faciliter les opérations de manutention, destockage, de transport et de distribution des marchandises.Exemples : palettes, bullpacks
La fonction protection
L’emballage doit protéger le produit qu’il contient, leconsommateur/utilisateur qui va le recevoir, et l’environ-nement dans lequel le produit sera utilisé. Exemples :bouteilles, boîtes de conserve, …
La fonction information
L’emballage doit fournir une réponse à toutes les questions envisageables sur l’origine, la composition, la manutention, le transport et l’utilisation du produit. C’est pourquoi différents types de marquages sont retrouvés sur les emballages : le marquage commercial, le marquage de sécurité, le mode d’emploi et les mentions légales obligatoires. Exemples :étiquettes classiques, étiquettes RFID (Radio Frequency Identification), …
La fonction marketing
L’emballage, unique lien entre le consommateur/utilisateur et le fabricant, doit attirer le client, l’inviter à s’intéresser auproduit. Exemple : suremballage, …
Choix d’un emballage
le choix d’un emballage est aussi une décision importante car il conditionne les modes de transport retenus et doit d’autre part protéger contre les différents risques que court la marchandise pendant le transport :
- perte ;
- avarie (coup de fourche de chariot, écrasement, chute, etc.) ;
- mouille (pluie, embruns, inondations, humidité, etc.) ;
- chaleur ou froid ;
- vol (25 % des avaries à l’international).
Ces risques doivent être évalués par rapport à la nature de la marchandise, aux destinations prévues, aux modes de transport envisagés et à leurs ruptures de charge.
Un envoi par camion vers une plate-forme de distributeur à quelques centaines de kilomètres en France ne demande pas le même emballage qu’un envoi par bateau vers un pays africain avec rupture de charge au port de chargement et déchargement.
Cependant s’il s’agit de transporter des produits de grande valeur (cartes téléphoniques, téléphones mobiles, etc.), il est évident que des précautions particulières doivent être prises même pour un simple trajet en France
Les conséquences de la réalisation de ces risques peuvent être importantes :
- perte de la marchandise non remboursée par le transporteur ou l’assureur s’ils prouvent que la perte résulte d’un défaut d’emballage ;
- obligation de livrer le même produit au client par le moyen le plus rapide et donc coûteux ;
- perte d’image de marque et insatisfaction du client.
Une bonne protection contre ces risques coûte plus ou moins cher ; elle s’obtient par :
- un choix d’emballage et la qualité de sa réalisation ;
- la certification éventuelle de l’emballage pour éviter qu’on l’accuse en cas d’avarie ;
- une assurance d’autant plus chère que les risques sont plus grands (bonus possibles).
Il arrive que des entreprises de distribution ou même de petites entreprises de production se refusent à utiliser d’autres emballages que les emballages d’origine des matériels qu’elles distribuent, ce qui est économique mais peut être à la fois une perte de temps importante pour devoir adapter des emballages aux colis qu’elles réalisent et une perte de qualité pour le transport et la manutention.
On notera par ailleurs que dans le cas d’avaries, les transporteurs peuvent mettre en cause la qualité de l’emballage pour se libérer de leur responsabilité.
C’est le cas particulièrement en transport international. La protection du donneur d’ordre est alors de pouvoir exciper d’une certification d’emballage. Par ailleurs la qualité de l’emballage joue sur les coûts de transport, de stockage, de manutention et aussi d’assurance.